Alright, let’s talk about that light. You know the one – the little oil can symbol, maybe angry red or ominous amber, flickering on your dashboard instrument cluster. It’s a sight that can instantly knot your stomach, sparking visions of expensive engine repairs. And while sometimes that fear is valid, quite often, the issue isn’t a catastrophic failure waiting to happen, but rather a faulty messenger: the oil pressure sensor.
This small but mighty automotive sensor is a critical component in your vehicle’s monitoring system. Think of it as the security guard for your engine’s lubrication system. Its main job – its unique attribute, really – is to measure the hydraulic pressure of the engine oil and report back. When it works correctly, you probably never think about it. But when it fails? It can trigger false alarms, causing unnecessary stress, or worse, fail to warn you if there is a genuine, engine health-threatening low oil pressure situation. Ignoring sensor failure symptoms just isn’t a great strategy.
The silver lining? Replacing a faulty oil pressure sensor is often a very achievable DIY auto repair. Doing this maintenance task yourself offers the double benefit of saving cash compared to shop labor rates and gaining that sweet satisfaction of fixing your own car. I’ve changed a few in my time, and while some are straightforward, others definitely test your patience!
This guide will walk you through the essential steps of the how to change oil pressure sensor process. We’ll cover what it does, why it fails, the tools you’ll need, the step-by-step replacement, and crucial checks afterwards. Ready to potentially silence that warning light and learn a bit more about your vehicle? Let’s get started.
What Exactly IS an Oil Pressure Sensor and Why Does it Fail?
So, what’s this sensor actually doing down there in the engine bay? In simple terms, as your oil pump circulates oil throughout the engine to lubricate and cool vital parts, the oil pressure sensor monitors the pressure within those oil passages (galleries). It converts this physical pressure into an electrical signal.
You might hear different terms used – oil pressure switch, oil pressure sender, or sending unit. Generally:
- An oil pressure switch is simpler. It acts like an on/off button, typically just triggering the warning light on your dash if the pressure drops below a set threshold.
- An oil pressure sender or sending unit is more sophisticated. It provides a variable signal (often by changing electrical resistance) that allows the dashboard instrument cluster to display an actual pressure reading on a gauge, or sends more detailed data to the engine control unit (ECU) / powertrain control module (PCM).
Knowing which type your car has helps, but the replacement process is usually very similar. It’s important to remember the potential for confusion here – this isn’t a MAP sensor (manifold pressure) or a fuel pressure sensor; its world revolves solely around engine oil pressure. Its name is straightforward: “sensor” comes from the Latin sentire (to feel/perceive), fitting its function perfectly.
Why do these sensors go bad? Like any electrical component on a car, they live a hard life. Common causes include:
- Internal Wear: The internal diaphragm or mechanism simply wears out over time.
- Contamination: Sludge or debris in old oil can clog the sensor’s small orifice.
- Electrical Gremlins: Corrosion on the electrical pins/terminals or issues with the wiring harness connector.
- Leaks: The seal (like a sealing washer or O-ring) can fail, causing oil leaks around the sensor body.
- Heat and Vibration: Constant exposure takes its toll.
Crucially: Before you condemn the sensor, verify the symptom isn’t actual low oil pressure! A flashing low oil pressure light or a gauge reading zero demands immediate attention.
Low oil is the most common cause of low pressure. Also, listen for any unusual engine noises (knocking, ticking). If the oil level is good but the light stays on or the gauge reads strangely (an erratic gauge reading), then the sensor becomes a prime suspect. Sometimes a check engine light might accompany the oil light, and an OBD-II scanner tool can pull specific diagnostic trouble codes (DTCs) pointing towards the sensor circuit. The goal is to replace a failed sensor, not ignore a real engine problem (the opposite of a functioning sensor).
Gearing Up: Tools, Parts, and Finding the Target
Okay, convinced the sensor is the likely culprit? Let’s gather our supplies. Having the right tools makes this job much smoother.
- Essential Tools:
- Socket set with ratchet and likely an extension bar. You’ll almost certainly need a deep socket that fits the sensor body. Sizes vary widely, so having a set is best.
- Wrench set (combination wrenches might be needed if a socket doesn’t fit).
- Torque wrench (Absolutely crucial for proper installation!).
- Rags or shop towels (expect some oil spill).
- Oil drain pan to catch that spill.
- Safety glasses and gloves.
- Maybe some penetrating oil if the old sensor looks rusty or seized.
- Possibly Needed Tools:
- Jack stands, car jack, wheel chocks (if you need to get underneath).
- Small flathead screwdriver (for the electrical connector tab).
- Brake cleaner (for cleaning the area before removal).
Next, the replacement sensor. Don’t just grab any sensor! They are vehicle-specific. Get the part number from your owner’s manual, the old sensor itself (if possible), or use your VIN at an auto parts store or online retailer. Decide between OEM and reputable aftermarket brands. Critically, check if the new sensor comes with a new sealing washer or O-ring. If not, buy the correct one separately! Reusing the old seal is asking for leaks.
Now, the hunt for the sensor location! This can be the trickiest part. Common attributes place it screwed into the engine block, often near the oil filter housing, or sometimes on the cylinder head. Some cars make it easy; others hide it behind other components. “My advice?
Do a quick online search for ‘[Your Car Model Year] oil pressure sensor location’ – chances are, someone’s posted a picture or video.” A repair manual (like Haynes or Chilton) is invaluable here. Be aware of rare attributes – occasionally, they might be integrated into another part.
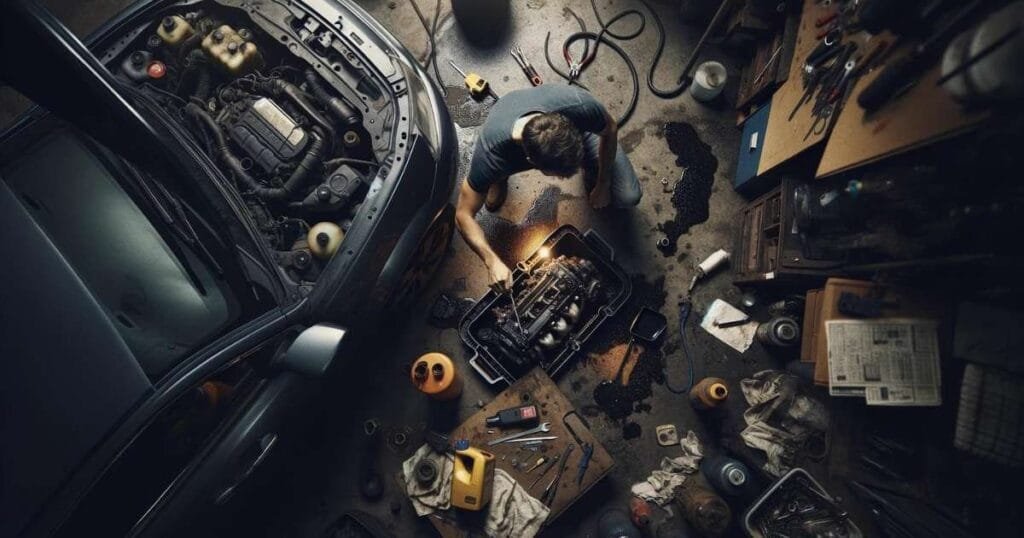
The Main Event: Your Step-by-Step Oil Pressure Sensor Swap
Got everything ready? Let’s perform the engine oil pressure sensor swap.
- Safety First – Disconnect Battery: Seriously, don’t skip this. Locate the negative battery terminal (usually marked with “-” or “NEG”). Use the correct size wrench to loosen the clamp nut, then lift the cable off the terminal post. Tuck it aside so it can’t accidentally reconnect. This protects you and the vehicle electrical system.
- Access the Sensor: Remove any covers or components blocking your path. Keep track of fasteners.
- Disconnect Electrical Connector: Carefully examine the electrical connector on the sensor. Find the locking tab, depress (or lift/slide) it, and gently pull the connector straight off. Never pull by the wires! Inspect the connector’s electrical pins/terminals for corrosion.
- Prepare for Spillage: Position your oil drain pan directly underneath the sensor. Some oil will come out.
- Remove the Old Sensor: Select the correct size deep socket that fits the sensor’s hex head or body. Attach your ratchet, adding an extension bar if needed. Turn counter-clockwise (lefty-loosey). If it’s stuck fast, apply penetrating oil where the threads meet the engine and wait 10-15 minutes before trying again. Apply steady force. Once loose, unscrew it the rest of the way by hand. Have rags ready! Check that the old sealing washer or O-ring came off with the sensor.
- Prep the New Sensor: Compare the new sensor with the old sensor. Confirm threads and connector match. Now, the sealant question:
- Does it have pre-applied sealant on the threaded portion? If yes, usually no extra sealant needed.
- Does it use an O-ring or washer seal? If yes, generally do not use thread sealant or Teflon tape on the threads.
- Bare threads, no seal? Use a small amount of appropriate liquid thread sealant or Teflon tape, starting 1-2 threads back from the tip. Don’t overdo it! Check your manual if unsure. “Getting this wrong is a common mistake leading to leaks or bad readings. When in doubt, follow the manufacturer’s recommendation for your specific part!” Ensure the new sealing washer or O-ring is correctly installed on the sensor.
- Install the New Sensor: Carefully thread the new sensor in by hand. It should go smoothly. If it binds, back it out and restart straight. Hand-tighten first.
- Torque to Spec: This is critical for preventing engine damage from leaks or sensor damage. Find the torque specification for your vehicle’s oil pressure sensor. Set your torque wrench and tighten until it clicks or indicates proper torque. Precision prevents problems!
- Reconnect Electrics: Push the electrical connector back onto the sensor until it clicks securely. Give a gentle tug to confirm.
- Reassemble & Reconnect Battery: Reinstall any parts you removed. Finally, reconnect the negative battery terminal and tighten the clamp nut.
Moment of Truth: Post-Installation Checks
You’re almost there! Now, let’s verify your work.
- Start the Engine & Check for Leaks: Fire up the engine. Immediately look closely around the new sensor base for any signs of oil seepage. Let the engine run for a few minutes, keeping an eye on the area.
- Monitor the Dash: Watch the dashboard instrument cluster. The oil pressure light should go out within a few seconds. If you have a gauge, it should rise to a normal reading (check your manual for typical pressure ranges at idle and cruising speed). The goal is a correct reading, the opposite of the faulty one you presumably had.
- Clear Codes: If you have an OBD-II scanner tool, now is a good time to clear any DTCs related to the oil pressure sensor circuit that might have been stored.
- Test Drive: Take the car for a short drive, monitoring the light/gauge and listening for any unusual sounds. Check for leaks again when you return.
What if the light stays on or the gauge is still acting up? Double-check the electrical connection first. Ensure you used the correct sensor. If those are okay, you might need further engine diagnostics – the problem could lie in the wiring, the gauge itself, or, unfortunately, there might be an actual oil pressure issue unrelated to the sensor. Troubleshooting sensor issues sometimes goes beyond simple replacement. Driving with a confirmed actual low oil pressure condition is incredibly risky.
Wrapping Up
And that’s the process! Replacing an oil pressure sensor is a task that ranges from surprisingly simple to moderately frustrating, largely depending on the sensor location. But by following these steps, using the right tools like a torque wrench, and paying attention to details like thread sealant application (or non-application!), you’ve likely fixed the problem and saved yourself some money.
More importantly, you’ve taken an active role in your vehicle maintenance. Understanding these engine sensors and how they contribute to the overall health of your powertrain is empowering. You successfully navigated the how to change oil pressure sensor challenge!
Remember, though, safety first. If you ever feel unsure or encounter a step that seems beyond your comfort level or toolset, don’t hesitate to consult a trusted professional mechanic. But for many drivers, this is a rewarding piece of DIY auto repair that keeps your engine monitored and happy. Well done!